Visual Inspection
New brass cups are inspected visually for imperfections.
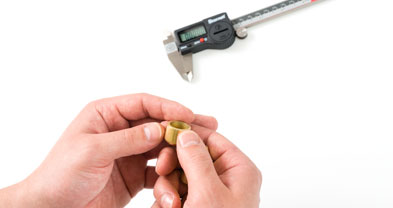
Stringent Testing. Maximum Quality
New brass cups are inspected visually for imperfections.
Dimensional checks are performed on the new brass cups.
The weight of the brass cups is verified.
The chart below displays the metallurgical composition of the brass cups.
Copper | 72.8000% |
Zinc | 27.1000% |
Nickel | 0.0210% |
Lead | 0.0081% |
Iron | 0.0075% |
Bismuth | 0.0040% |
Antimony | 0.0027% |
The photo below shows the brass cup’s grain structure.
Photo courtesy of George F. Vander Voort
A technician verifies the hardness of the brass cups.
Drawn brass cups are visually inspected for imperfections.
Drawn brass cups are measured to confirm proper dimensions.
The thickness of the wall of the drawn brass cup is measured verify accuracy.
The hardness of the drawn brass cup is measured to ensure quality.
A tech uses a microscope to check the grain structure of the drawn brass cup.
The exterior dimensions of the casing are measured to verify accuracy.
The primer pocket is measured to ensure accurate manufacturing.
The cartridge is weighed to verify manufacturing specifications.
The internal volume of the cartridge is measured and verified.
A technician confirms the proper thickness of the cartridge’s webbing.
A technician verifies the neck concentricity of the cartridge.
A technician measures the hardness of the casing to ensure safety.
The casing’s maximum internal pressure is tested to ensure safety.
The casing is tested in a firearm to verify functionality.
A technician dissects the final case to allow him to verify the internal dimensions.
Casings are tested to verify they have no residue after manufacturing and washing.
If you'd like to learn more about our QA process, or have questions on any other technical resources, let us know.
By entering this website, you certify that you are 18 years of age or older.